サマリ
想定読者:設計業務に興味がある方 / 想定時間:15分~20分程度
第17回目のテーマは、基板製造について取り上げます。
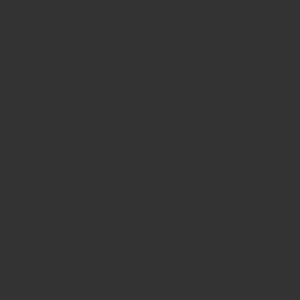
#1 基板の製造まで打ち合わせを重ねる
私が勤めていた会社ですと基板製造は外注していましたので、製造メーカさんと密に連携してやり取りしていた視点から記載します。
前回も記載しましたが、初期の段階で基板の材質や性能におけるシミュレーションなどを相談(依頼)します。高速な信号を取り扱うほど基板の材質に気を付けなければなりませんし、部品点数が多い=配線数が多い場合には複層基板にしなければならず、コストとの兼ね合いになる部分です。ここは過去実績を元に製造メーカさんと打ち合わせを実施して決めていきます。
設計が進んでいくと、徐々に回路全体のサイズや形がわかりますので、基板割(1枚の板からどのように基板を何枚取るか)を検討します。変な形の基板ですと、余分なスペースが多くできてしまい1枚の板から取れる枚数が減ってしまうため、形や配置する向きにも注意します。特に、基板を1枚1枚取り外す際に基板を物理的に割るのですが、変に割れないように”マチ”を確保しなければならないことや、端にはテンションがかかるため、ある程度離さなければならないなど、思った通りには枚数が取れないことがありますので、複数種の基板を組み合わせて1枚にするなど様々な工夫を凝らして対応しています。
その後、回路図・BOM・パターンレイアウトを適宜連絡し、基板イメージをすり合わせていきます。基本的には中間時点でのラフ案と最終案の2パターンで済むことが多いです。
結構頭を悩ませるのが、(特殊部品など)支給品がある場合には製造日までに送付しなければなりません。設計が完璧には定まっていない中、長納期部品はリードタイムの都合、先に発注して確保しておかなければならず、期日を逆算すると全然時間がないことがほとんどです。設計は常に時間との戦いを強いられているのはこの部品納期が主に原因だと言っても過言ではありません。良く使う汎用部品(抵抗やコンデンサなど)はリールで支給することやメーカ在庫から使うことも一般的ですので、こちらは特に心配することはないです。(ただし、コンデンサ不足の時期は大変でした、、、)
#2 基板の製造を待つ
基板製造はノウハウを保有している(また、お付き合いの長い)製造メーカに依頼します。基板の製造過程は製造メーカさんがわかりやすいサイトを掲載していますので、そちらのリンクを貼ります。(また最近では動画でもわかりやすいのがありますね)
※調べていたところ、”システムギア”さんの以下のサイトがわかりやすいためおすすめです
プリント基板製造工程|システムギアダイレクト
簡単に流れを記載すると、まずは回路上で導通する箇所(シルク)の設計を実施し、銅箔の乗った基板に印刷。その後、印刷していない箇所の余分な銅箔を落とし(エッチング)、不必要な箇所に半田が付かないように膜を貼ります(ソルダーレジスト)。これらを繰り返して回路を作っていき、最後に表面加工(フラックス塗布など)をして、部品を機械もしくは手作業でマウントするなど半田づけを実施して、ようやく基板が完成します。(簡単にまとめてもこれだけの量ですので、大変な作業ですね)
この間、設計者としては、製造期間中にテスト仕様書を作りこみます。当然頭の中にチェックしなければならない仕様は浮かんでいれど、基板の製造開始日がクリティカルパス(遅れるとプロジェクトの遅延に直結する)により、回路設計/パターンチェック/部品支給とフル稼働で対応しています。データや部品支給が完了すると後は待ちになりますので一息つけます。本当は休みたいところですが、基板製造の待ち期間中に、テスト仕様書を、もうテスト結果が書き込めるレベルまで仕上げていき基板を待ちます。V字モデルをご紹介した回でも記載しましたが、基本的に設計仕様、要件通りに動くかをチェックしますので、漏れが無いように整理します。
#3 初期不良チェック
基板が届いたら、作りこんでいたテスト仕様書を元に、まずは初期不良チェックを実施します。もちろん製造メーカさん自体が実施していますが、設計者目線からもチェックは欠かさずに実施します。具体的には、少なくとも以下の3つを実施しています。
①マウントした部品に異常がないか
たまにマウントした部品がずれていたり、よくあるミスとしてはダイオードなど極性がある部品が逆についていることがあります。これはマウントミスの場合もあれば、そもそもCADの配置ミスの場合もあります。導通時に最悪の場合には他の部品が壊れることもあるため念入りにチェックします。
②半田のノリをチェック
あまりケースとしては少ないですが半田のノリが悪い部品をチェックします。こちらがあると一見つながっているように見える部品が実はつながっていないこともありますので、注意してチェックします。
”小山高専の技術室”のHPにとても良い図がありましたので引用します。良い半田は富士山型になっているのですが、のりが悪く部分的にしかついていないことがたまにあります。(悪い半田)
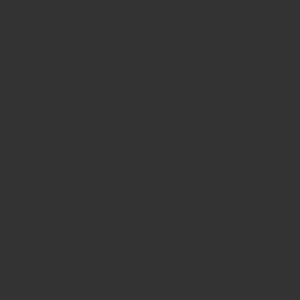
小山工業高等専門学校, 教育研究技術支援部, 技術室より(https://www.oyama-ct.ac.jp/tso/workshop/soldering/soldering_2.html)
③抵抗値の確認による導通回路部分をチェック(電源周りや、絶縁が必要とされる箇所は念入りにチェック)
①②を元に目視でのチェックを完了した後に、テスターを使って導通チェックを実施します。当然同電位の箇所は1オーム以下の状態になっているべきですし、別の電位箇所とは∞に近い抵抗値が出ているべきなので確認します。
このチェックでなぜか値が不安定になっており、よくよく調べると①に記載している”部品が逆についていた”などがわかることもありますので、念入りにチェックします。特に、電源周りに異常が無いことがチェックできれば、導通しても問題ない(少なくとも壊れない)ことが保証されるため、時間をかけてでもここは念入りにチェックします。
このように①②③をチェックして、問題なければ導通した回路テストへと進みます(次の記事で記載します)